3D Vision-Guided welding parts grab out of orde
Project background: In recent years, the traditional automobile industry seeks to upgrade, new energy vehicles continue to develop, and the transformation of the automobile industry has spawned a large number of automation needs. High transformation standards, complex processes, and a wide variety of workpieces are long-term challenges for automation in the automotive industry. All kinds of typical transformation, such as workpiece loading and unloading, positioning assembly, etc., have high requirements for technical indicators such as rhythm, accuracy and stability. The new generation of vision solutions based on the DexForce intelligent DexVerse™ embedded intelligent engine can effectively cope with complex conditions such as a large number of workpiece types, surface reflections, complex structures, disordered stacking, and ambient light interference.
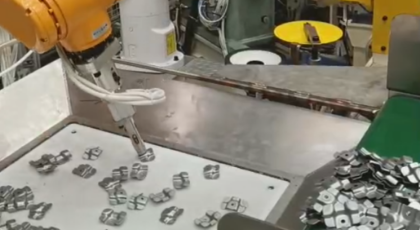
- Project advantages:
- The DexForce intelligent DexVerse embodied intelligent engine is used for data generation and annotation, and the trained model parameters are few; And exclusive support to provide CAD can quickly train new algorithm models, compatible with a number of different types of workpiece, support flexible production change. Greatly reduce the work intensity of front-line operators, can improve production efficiency and reduce costs.
- Support to configure multiple product models at the same time, and switch operations according to robot signals; There is no need to stop production to collect annotated data, and the deep learning model training of the new workpiece can be completed in 8 hours, and the production can be quickly launched.
- Zero code, zero programming, direct adjustment of parameters can achieve visual positioning, the fastest 5 minutes to complete visual configuration, 20 minutes to cooperate with the robot to grasp debugging.
- Application results
In this terminal automobile factory, DexForce 3D vision system was introduced to complete the automatic loading and unloading operation of nut welding and other workpieces at the grasping station of its welding workshop, and multi-model flexible switching grasping was realized. The construction cost and utilization rate of the station have been greatly optimized, and it has been stably put into production, thereby reducing the time and labor force of manual operation, shortening the production cycle and improving production efficiency.