Industry insight | With intelligent response, DexForce intelligence to help the automotive industry "shift speed"
As a master of industrial civilization, the mature automated production line of the automotive industry has been a model for learning in all walks of life. However, under the influence of internal and external factors such as cost pressure, product structure adjustment and intelligent and artificial intelligence applications, traditional production methods are facing a new round of changes.
Auto parts of the workpiece loading and unloading, positioning assembly and other links, the rhythm, accuracy, stability requirements are particularly harsh. Although the application of industrial robot arms has been relatively mature, with the increasing demand for flexible production in the supply chain of the automotive industry, new requirements have been put forward for the application of vision systems, especially 3D vision technology.
DexForce Intelligence relies on the self-developed DexVerse™ embodied intelligent engine to create a soft and hard integrated 3D visual guidance solution to help the automotive industry “shift up speed” and move towards the intelligent fast lane.
One-click connection from CAD import to model training
In the field of auto parts, the traditional appearance of incoming materials is complex and changeable, and the conventional visual template matching method is difficult to meet the needs. To solve this problem, many deep learning algorithms are used in the industry. However, the traditional deep learning path often needs to borrow products from customers for data collection, manual handling and collection, and then return to the manufacturer for annotation training, and finally send the trained model to the user.
This 3D vision solution faces the pain points of difficult data acquisition, cumbersome collection and annotation work, high labor cost, long cycle, at least two or three days, more than one week, difficult to achieve product and scale application, which seriously affects the efficiency of the automotive industry.
Based on this, cross-dimensional intelligence provides a more efficient and convenient solution.
Through the use of CAD files to generate a large amount of synthetic data, in the simulation space to simulate a variety of products in various production environments, various product quantities of various gestures, and training, no need to approach to collect/label data, only provide CAD to complete the model training. When new workpieces appear on the generation site, model training can be completed through the engine with one key, achieving an efficient new product adaptation process, truly based on user needs, oriented to industry pain points, and releasing industrial productivity.
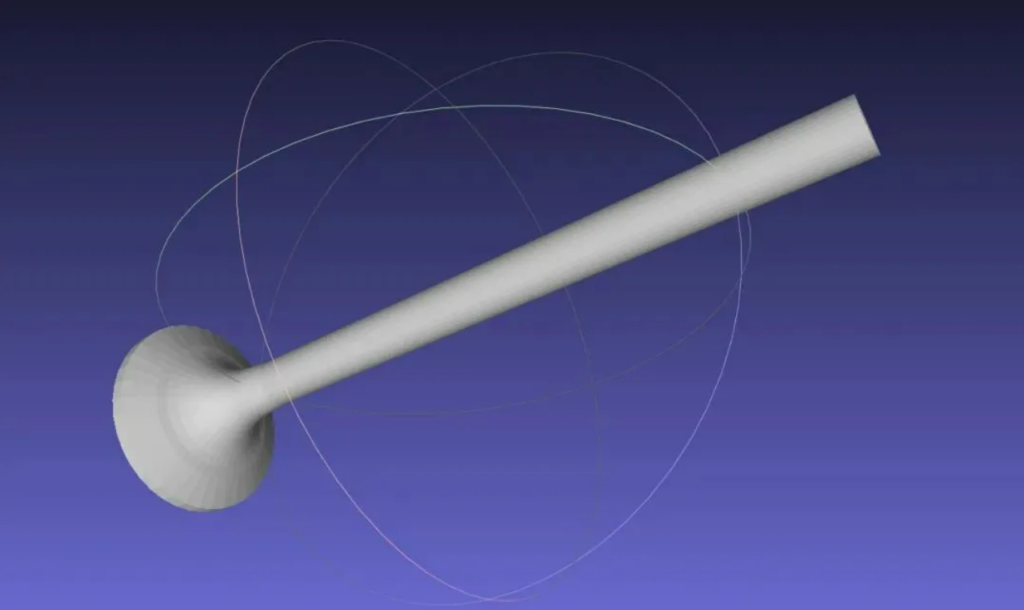
Car door core CAD model import
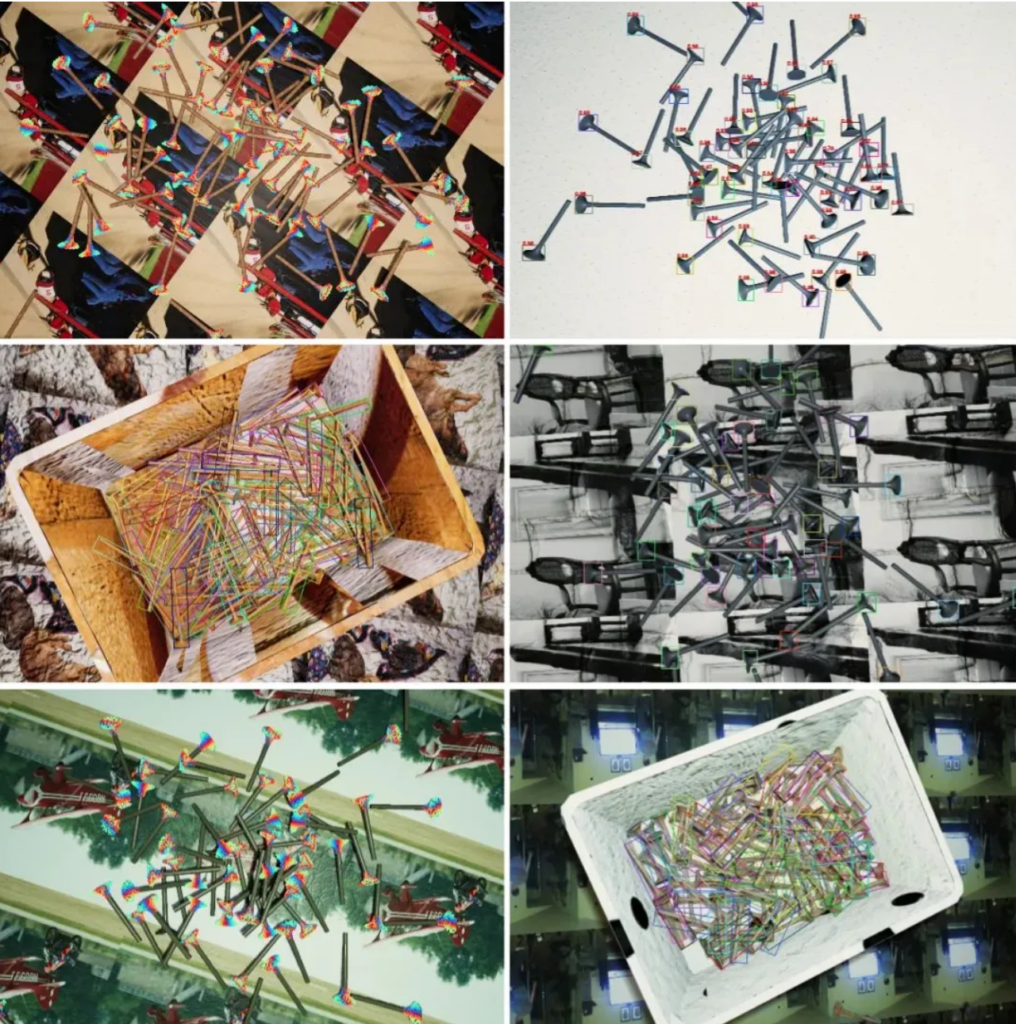
Car door core training data generated by DexVerse™
Unlike the traditional AI+3D approach, the solution of DexForce intelligence supports the direct import of CAD files and the training of deep learning models with one click. In the data acquisition process, DexVerse™ is used to synthesize data, which greatly improves the collection efficiency of training data. The data generated in the simulation environment covers almost all possible conditions and has a high diversity, which makes the recognition effect of the model optimal. In addition, the model has a wide range of generality, applicable to various environments and application scenarios, and greatly improves the efficiency of subsequent similar scenarios.
Anti-interference "eyes" boost upgrade and transformation
In addition to the difficulties of data acquisition and labeling, another major challenge facing the automotive industry in the process of using 3D vision is how to identify a large number of highly reflective parts in a strong light environment.
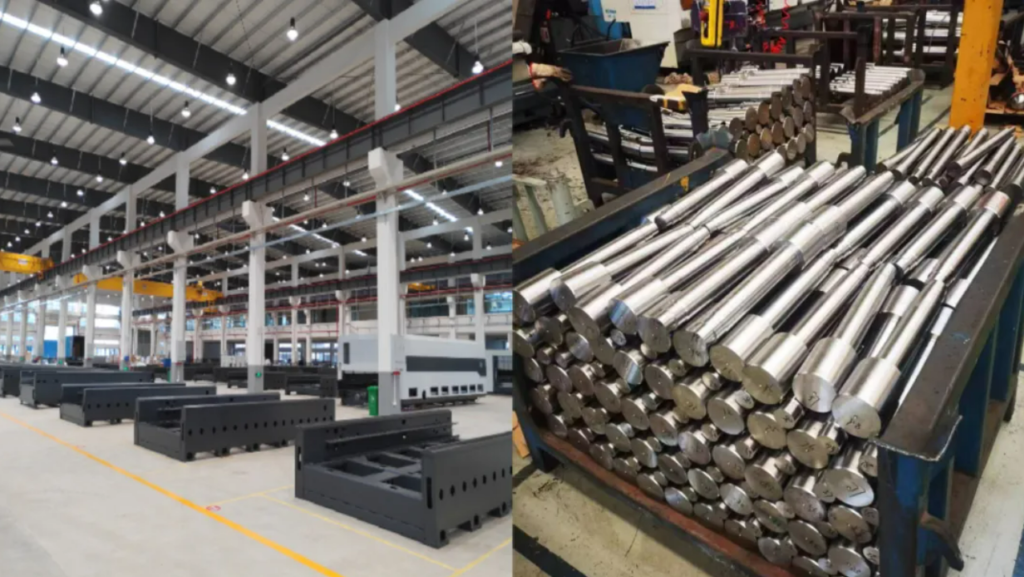
At present, structured light camera is widely used in industry, but due to the limitation of its technical principle, the coded pattern projected in the strong light environment is easy to be flooded by natural light. At the same time, the characteristics of highly reflective workpieces also cause traditional structured light cameras to produce poor quality point clouds in these scenes, or require longer imaging times, seriously affecting the grasp accuracy and production efficiency.
In order to solve the problem of high inverse workpiece point cloud imaging in strong light environment, cross-dimensional Intelligence launched the Kingfisher binocular stereo intelligent camera.
Unlike the imaging principle of traditional structured light cameras, Kingfisher cameras do not need to actively cast light, only by simultaneously capturing two sets of 2D images, combined with Sim2Real-trained point cloud reconstruction model, can quickly generate workpiece point clouds. Even under intense ambient light, the camera was able to reconstruct a three-dimensional point cloud of the scene in 0.5 seconds. In principle, this avoids the imaging limitations of traditional structured light cameras, and is especially suitable for outdoor strong light, high-reflective parts loading and unloading scenes.
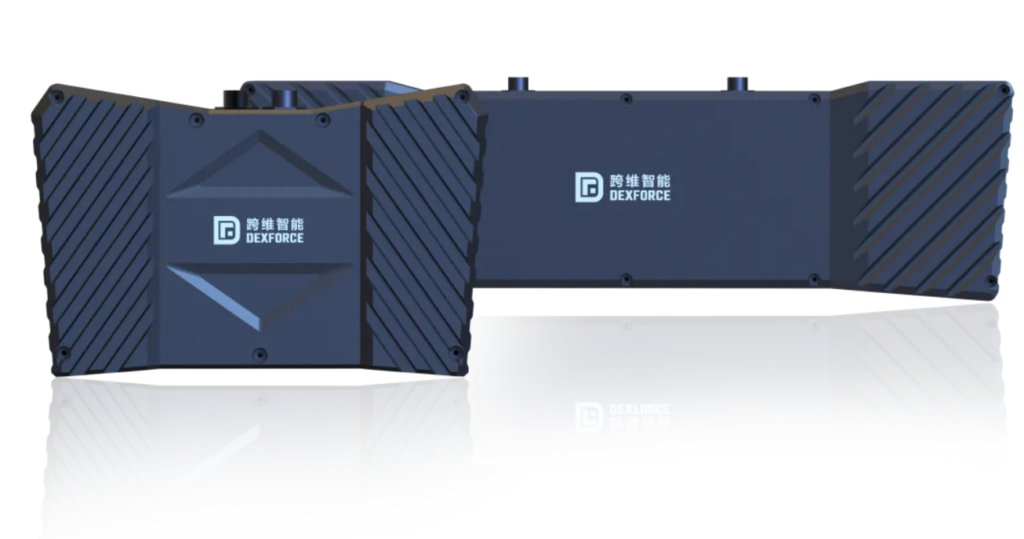
For example, in the alien wheel grab loading link of a large auto parts factory, due to the existence of strong light environment in its automobile manufacturing workshop, and the surface of the alien wheel is finished, the process is very bright and there is anti-rust oil, which poses a challenge to the quality of 3D vision imaging, and the traditional structured light camera is difficult to strike a balance between cost, efficiency and accuracy. The cross-dimensional Kingfisher binocular intelligent camera can accurately complete high-quality imaging of the alien wheel under bright light conditions. The overall visual beat of the project can reach 5s, the comprehensive grasping accuracy is less than ±3mm, and the grasping success rate is greater than 99.9%.
At present, cross-dimensional intelligent DexSense high-precision 3D imaging and sensing equipment series, including Kingfisher binocular stereo intelligent camera, Xema Arctic Gull series open source camera and Sparrow series lightweight DLP monocular structured light camera, have been widely used in the automotive and auto parts industry.
In addition to the automotive industry, the cross-dimensional intelligent 3D vision guided grasp solution has been applied in batches in semi-structured scenes in 30+ industries such as home appliances, industry, logistics, etc., with a success rate of more than 99.9% under the grasp/operation task with millimeter-level accuracy. At the same time, cross-dimensional intelligence is also steadily landing products in more structured and unstructured scenarios such as medical and commercial, contributing to the intelligent process of global customers.